Being a project manager in charge of planning, executing and delivering a successful project is a tough job. Using purchase orders in construction makes it easier.
Although project managers typically commit to projects that are properly estimated and planned, it’s far from uncommon to encounter several unexpected occurrences. This is doubly the case when the schedule is tight and some team members are involved with requesting parts or materials, all of whom are intent on meeting the deadline.
With so many people generating various costs and potentially delaying purchases, the project manager’s control can be severely limited. The last thing they need is unexpected project expenses resulting in overall costs getting out of control.
A transparent purchase order process is what helps project managers to stay in control over project spending.
Different sources of project costs
Project costs come from various sources –overhead costs, costs associated with contracts, material purchases, etc.
A number of costs are also associated with requesting purchases from vendors. Such one-off purchases are mainly carried out by different stakeholders at the site, and make up a significant amount of the overall project cost.
What is a purchase order?
A purchase order is a simple request to buy products or services from suppliers or subcontractors, typically sent via e-mail. This request states the amount of products or services needed and the purchase price.
Here is a basic e-mail purchase order example:
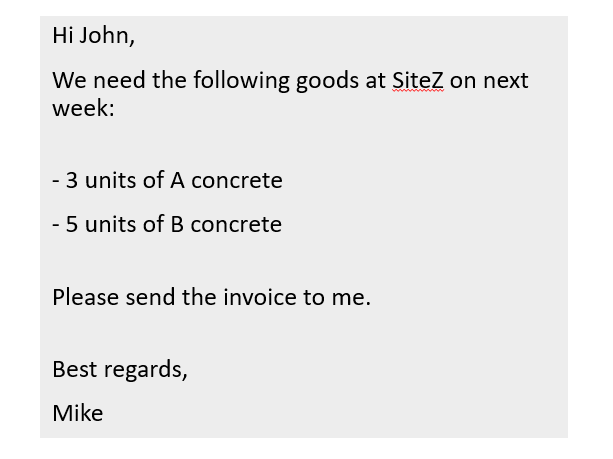
However, while sending a purchase order via e-mail sounds simple, the process is often inefficient and has the possibility of error. This is because orders are issued by different stakeholders, leaving project managers with little to no control over these orders and later leading to issues of checking whether or not the company bought what it’s faced with paying for.
Using purchase order software makes a difference
Sending a purchase order via a specific construction software is no different than sending it via e-mail – simply click “Create purchase order”, enter the articles you plan to buy and send it straight to the recipient’s e-mail.
At this moment, the newly sent purchase order becomes visible to the project manager. It’s clear when a purchase order was issued, by whom, and what the expected cost is of the purchased items.
This means you can now predict the future payment due for the requested items of which you know the planned cost.
The purchase order system allows the invoice to be submitted immediately following the purchase order, thereby allowing the project manager to easily make sure that the items on the invoice match the purchase order.
There’s no need for recurring data entry, and the project manager needs only review the invoice to check that it meets the purchase order before submitting it to accounting.
How to streamline project purchase orders?
The first thing to ask is, are we happy with our current purchase orders process? Does it provide us with the visibility we need? If the answer is no, the project manager may decide to streamline the purchase order process to better control project costs. In this case, it is important to do the following:
- Set financial limits. When a purchase exceeds a certain value, run a purchase order. For example, all purchases that exceed $1000 must be run through the established purchase order process. However, it makes no sense to run small-cost items through the process since these don’t make a significant impact on the overall cost.
- Decide on the platform for running the purchase orders. You can use a shared Excel file, or for easier use, purchase order software.
- Introduce the process to stakeholders and set rules for following it.
Have an organized purchase order process
A well-oiled, quick and efficient cost management process helps project managers stay on top of finances, making it easy to spot errors when they occur and take immediate action.