Background and before 2022
Construction costs have been on an upward climb for more than the last two decades. You can see that the construction prices in the EU have grown by 45% in the last 16 years. In general, there is a clear upwards trend with some steeper growths during some periods. Reduction in cost is only present during years when there was a recession. And even then, the reduction was for a very short time.
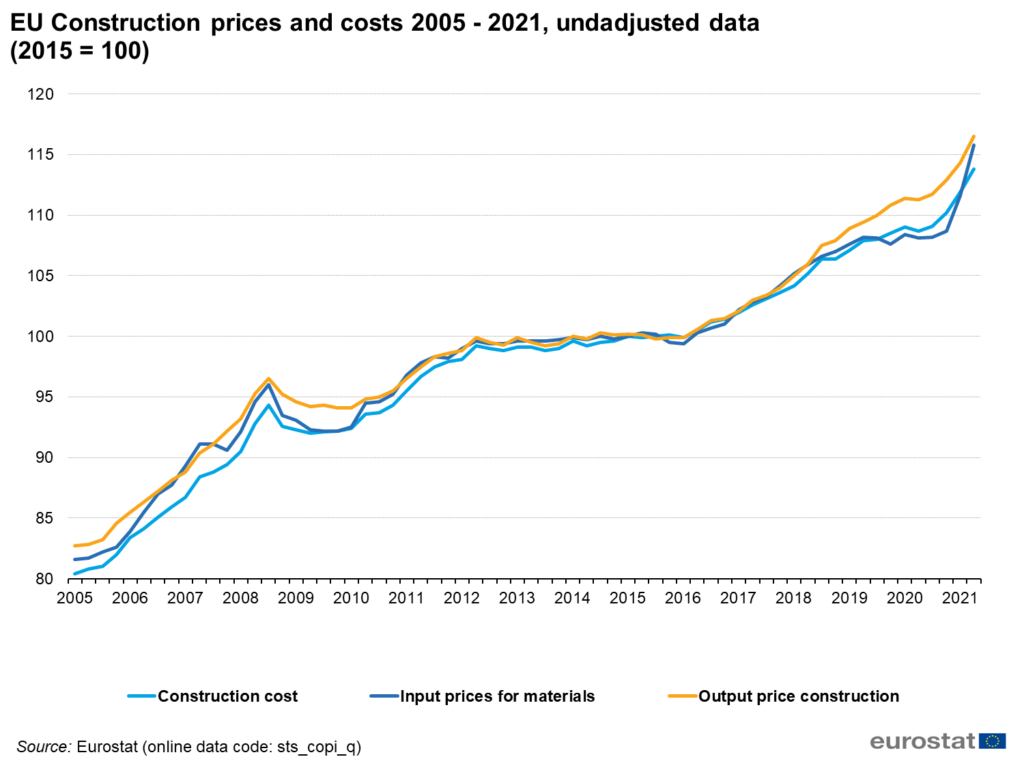
Reduced purchasing power
In the long run, this can partially be explained by the purchasing power of a currency going down. This is caused by inflation. In the long term, this is due to the supply of money growing too big relative to the size of an economy. Basically, if there is too much money in the market, everyone is able to pay more for the same goods. Thus, the price of one good increases, also allowing the price of other goods to increase.
On the picture below, you can see how the purchasing power of the US Dollar has changed throughout the years. We find that this graph really visualizes the inverse relation between currency value going down and the prices going up. This is a reason for the construction prices steadily increasing as well.
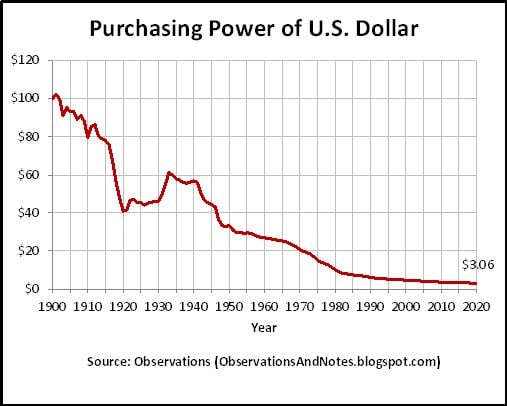
COVID-19
During the COVID-19 crisis that began in 2020, the macroeconomic problems causing price increases were quite a bit more specific. It wasn’t just long-term monetary symptoms of the choices by central banks. It had much more to do with reduced capacities in raw material mines, production sites, and challenges with logistics. Even up to 89% of respondents of a survey said that they are experiencing limited availability of raw materials.
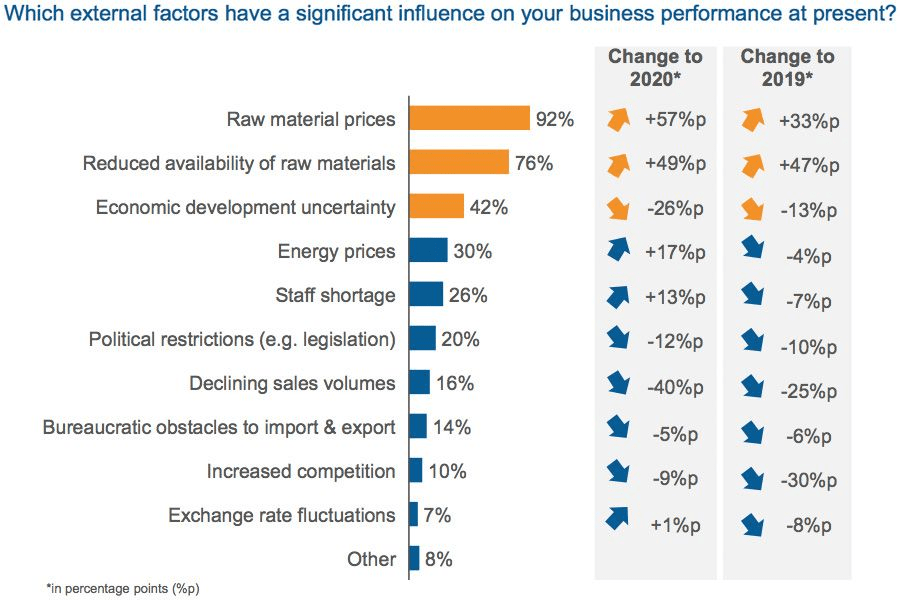
This data shows that instead of too much money on the market, there are too few amounts of materials available. The construction industry uses a lot of materials and it’s growing rapidly. From 1997 to 2007, the total amount of materials used in the EU for construction has grown by over 40%. From 4 billion tonnes to more than 5.6 billion tonnes.
COVID-19 also changed the labour demand and supply in the construction sector. At the beginning of the pandemic in April 2020, the number of unemployed construction workers in the US increased from 750 thousand to above 1.7 million. The number of April is expected to be underestimated, so the problem could be even worse than expected. As many of the people who were laid off found a job in different sectors, the supply of qualified construction workers dramatically dropped as well.
Living conditions improving
With the increasing standard of living in many countries globally, it is clear that this number is also in a growing trend for non-EU countries. The increased need for raw materials is also evident in the fact that the average size of a dwelling is also steadily increasing.
All of these factors are paving the way for the trend of long-term cost increases for construction materials and thus also the final prices of construction projects.
What changed in 2022?
The beginning of 2022 was optimistic as was the forecast at the end of 2021. Many experts claimed that productivity and construction volumes will bounce back to the pre-COVID levels and even surpass them by more than 3%. That was before we ran into various political issues that have prolonged the supply chain issues or even made them worse.
One way to get a holistic overview of the global supply chain status is to look at the Global Supply Chain Pressure Index (GSCPI) by Liberty Street Economics. This index indicates the troubles we are having with the supply chain. They even predict that the issues might be worsening in the near future.
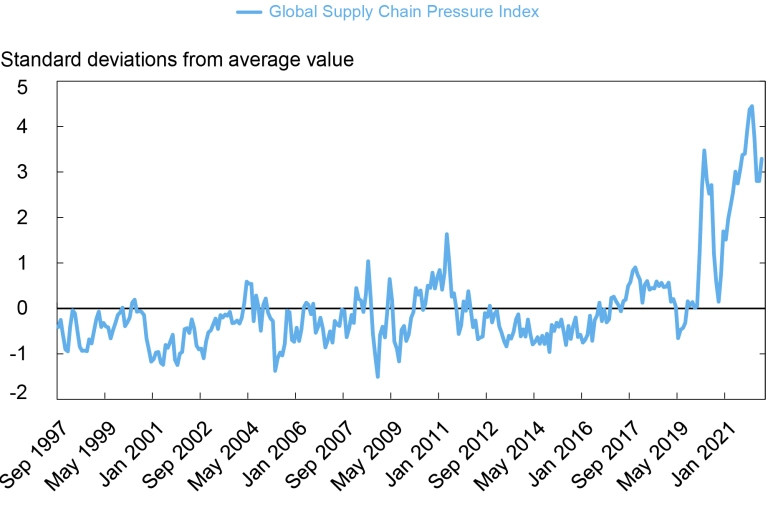
The war in Ukraine
The war in Ukraine is one of the main reasons for metal and fuel prices going up. It is said that Russia was a major exporter (3rd largest) of aluminium and copper. This means that since Western companies do not want to trade with an aggressive partner, materials need to be bought somewhere else.
Since Russia was usually a rather cheap place to buy the materials from, the scarcity of the materials is also supported by the higher prices of the other suppliers. Additionally to the raw metals, Russia is also a large exporter of energy sources. As trading with them reduces, the energy costs will also go up.
China and Taiwan tensions
After Nancy Pelosi visited Taiwan, China ramped up its military exercises around the island. The biggest of its exports are machinery, electrical machinery, and optical/medical instruments. More and more construction tools, equipment, materials, and software rely on high-tech chips. It is even claimed that Taiwan accounts for 92% of production for advanced semiconductors.
This means that a conflict in Taiwan can have very long-lasting effects on our everyday lives and especially on the more high-end workflows and processes in the construction sector. Setting up production factories for semiconductors will take a long time. That means that the prices for every gadget, that has some “smartness” in it, will go up.
The energy crisis getting worse
If we exclude the 28% of global energy needed for transport, then the building stage of construction still uses 5% of all energy. This means that the construction sector is highly dependent on fluctuations in energy prices.
For example, according to the Energy Policy from 1976, the amount of total energy needed to build a single flat in a large concrete block of flats is 265 GJ. This translates to approximately 73.6 MWh. With the average kWh price in the UK in 2022 being around 20 p/kWh, the total energy-based cost ends up at 14 720 pounds.
It is expected, that the prices will climb to around 51 p/kWh, which would bring the number to 37 536 pounds. It is not an insignificant change in the final price of the flat.
What are the main components of construction costs and where are they heading?
Construction is a very labor and material-intensive industry and can not really be drastically influenced by similar innovations as other fields – medicine, IT, etc. This means that any change in input prices will directly also affect the output price of the final product.
So let’s take a look at some of the direct reasons behind the increase in cost for construction projects.
Labor
The cost of living has soared massively due to inflation and this means that the salaries also have to match the new costs at some point. If you add the higher salaries up with the reduced amount of qualified workers that we mentioned in the COVID section before, you can see why labor is a big part of the costs.
Construction salaries grew by 6% from 2021 to 2022. It is very likely that it will keep rising for the next few years until automation can take over more.
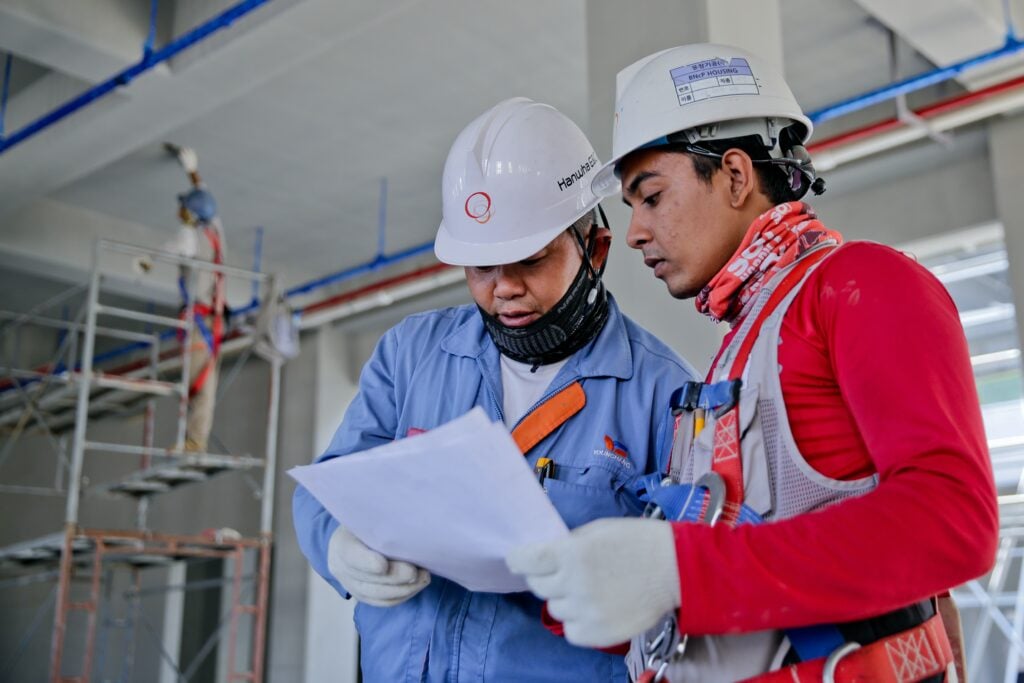
Cement
Cement is one of the main ingredients in modern construction projects. However, much of the global cement production is spread around the world – Vietnam, Turkey, Germany, etc. This means that any disturbance in supply chains will also cause issues with concrete. And if there are issues with access to concrete, the local supply prices will go up.
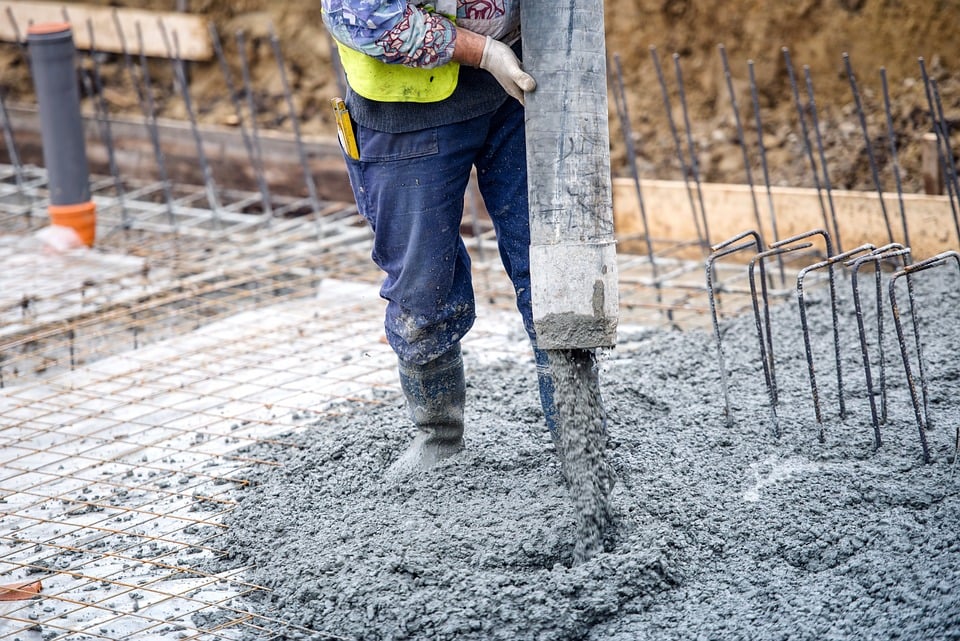
It is forecasted that the price of cement will increase by a further 7.7% in the second half of 2022.
Steel
We already touched on the issues with the availability of raw metals because of the Ukraine war. However, Russia also is one of the biggest exporters (5th largest) of iron and steel. This means that the current sanctions and reluctance in trading with Russia will cause prices to increase. Additionally, building out new supply chains is a lengthy process and will not show the results right away.
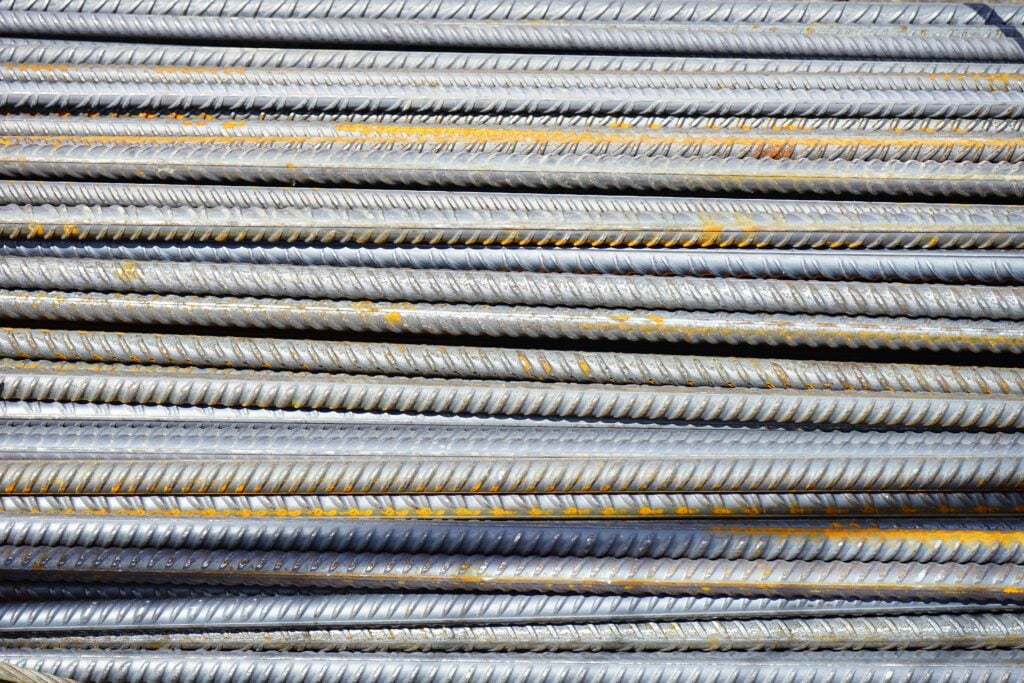
The price of steel did double right after the start of the Ukraine war but returned to pre-war levels at the end of July. It is expected that there will be reduced demand for steel in 2022 and the price will not increase so much.
Wood
The Ukraine war also causes issues for the accessibility of wood materials. Russia is the second largest sawn wood exporter in the world. This means that access to materials from there will be reduced and many might look for alternatives.

Similarly to steel, the price of lumber did shoot at the beginning of the Ukraine war but then went down to its pre-war levels. The price actually peaked in 2021. It is expected that the price of lumber will not rise as inventories are starting to pile up.
Stone
Stone is a big part of bathroom and kitchen countertop materials. Luckily, the largest exporters of stone materials are not involved in the Ukraine war. The larger exporters here are India, Brazil, and Norway. However, China is 4th in export volume and the Taiwan conflict might cause issues instead.
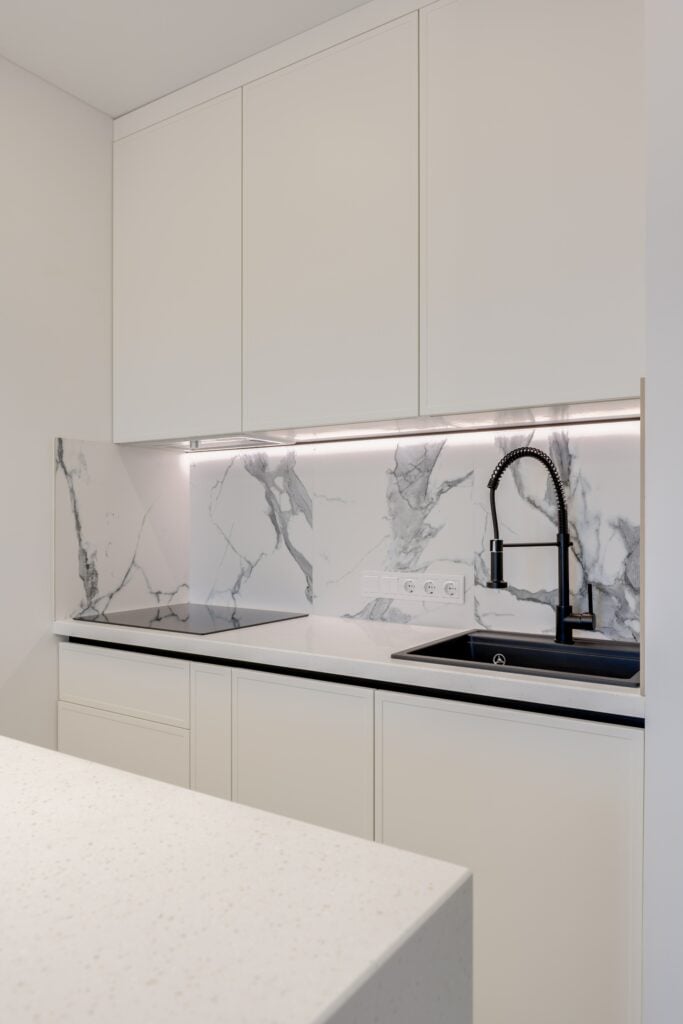
The price forecast for stone in 2022 is unclear at this point. We will update this part of the article in the near future.
Brick
Bricks have been used for a long time as it is a simple material to deal with. It is easy to shape and there are different types of mortars that also add to the flexibility. The top exporters of brick materials only include China as a potentially risky country. The other exporters are not included in the conflicts mentioned.
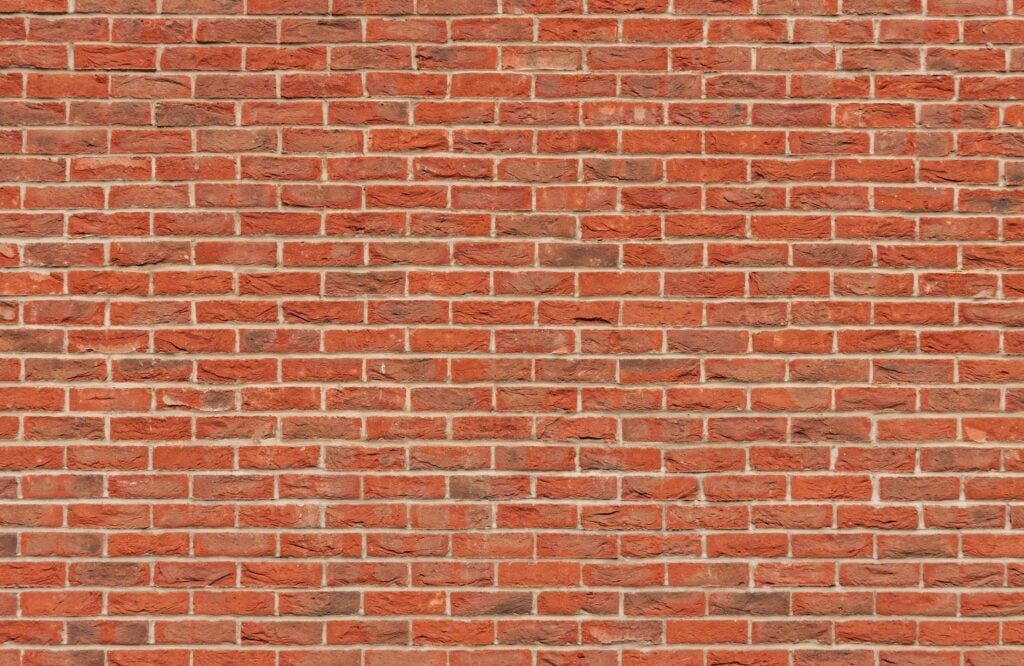
Many brick makers, including Forterra, have increased their prices in double-digit percentages. As bricks are not a commodity, it is difficult to estimate exact price increases.
Transport
As large amounts of materials have to be delivered to construction sites, the price of the delivery, directly and indirectly, will affect the final price of a building. In March 2022, the pre-tax price of diesel increased by 69% compared to the January level. With the war in Ukraine, many Ukrainian truck drivers returned to defend their country and made the driver shortage even worse than it was before.
As construction sites are rather distributed, the price of transport to the site will clearly be visible in the bottom line for the projects.
What might keep the costs up?
Ukraine war doesn’t stop
If the war in Ukraine does not stop any time soon, the material and transport-related issues will not be relieved any time soon. To be honest, they will also not improve even if the war ended today.
Many countries are rethinking their energy and material suppliers away from Russia. This means that prices will still go up and the availability of some materials will still go down.
Taiwan tensions escalate into a full-blown war
If there was a war in Taiwan, we would have issues in every aspect of our lives. Construction would also be affected, but it is possible that machines in other sectors – medical, public infrastructure, etc – would be more prioritized than construction.
A sad scenario could be that many construction machines would not have parts anymore to service them. Additionally, older and simpler machines could be brought out again just to relieve the issue. They would, of course, not be as productive as the latest and greatest.
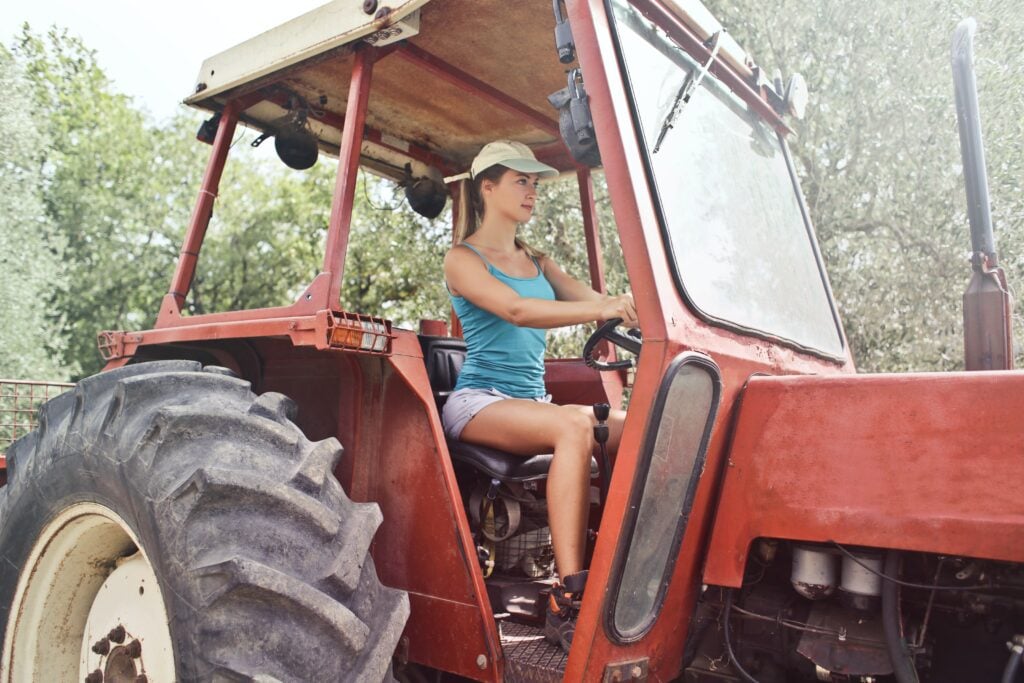
Supply chain issues don’t get resolved quickly enough
If international and intercontinental transport lines don’t become less overloaded, then the delays in delivering goods will cause the local demand to go up. The demand and scarcity will in turn cause the goods to increase in price.
This means that probably everything construction-related also goes up in price.
Conclusion
There are many different reasons why construction costs will probably continue to increase in the near future. If the military tension and conflicts will not ease up, then the costs will possibly continue to increase even more unpredictably than it has until now.
Luckily, some materials like wood and cement will probably stay at lower prices as the demand for them has reduced. The labor costs however will continue increasing at an ever-increasing speed due to inflation and will be a big part of why the final costs will also increase.
How can I forecast actual construction will construction costs go down in 2022?
We recommend construction companies of any size use construction forecasting software to keep track of their material and labor costs. This software often also tells you the project profitability.