Construction projects are intricate, multi-faceted endeavors involving numerous stakeholders, financial resources, and logistical challenges. Despite thorough planning, many projects experience construction cost overruns, where actual expenses exceed initial budgets. These overruns can lead to significant financial losses, delays, and strained relationships between contractors, clients, and investors.
Understanding the root causes of cost overruns and implementing proactive strategies can help mitigate these risks. This article will explore why cost overruns occur, provide real-world examples, and outline actionable solutions for contractors, developers, and project managers.
What Are Construction Cost Overruns?
A construction cost overrun occurs when the final cost of a project exceeds the estimated budget. Overruns can range from minor budgetary discrepancies to massive financial shortfalls, potentially making projects unviable.
Common Types of Cost Overruns
- Material Cost Overruns – Price fluctuations and supply chain disruptions.
- Labor Cost Overruns – Increased wages, overtime, or unexpected workforce shortages.
- Scope Creep Overruns – Additional work requested beyond the initial agreement.
- Regulatory Overruns – Unplanned costs due to new laws or compliance issues.
- Design Changes Overruns – Revisions and errors leading to additional expenses.
- Administrative Overruns – Inefficiencies in project approvals and contract processing.
- Technology Overruns – Higher-than-expected costs for software, automation, and other digital tools.
Common Causes of Construction Cost Overruns
1. Inaccurate Project Estimates
One of the leading causes of cost overruns is inaccurate estimates during the planning phase. Estimators may rely on outdated data or fail to account for inflation, resulting in budgets that do not reflect real-world costs.
Solution: Utilize advanced estimating software that integrates real-time market data and historical cost analysis. Conduct multiple cost estimation rounds and involve stakeholders in refining budgets.
2. Design and Planning Errors
Flawed blueprints, incomplete architectural designs, or misinterpretation of client requirements often lead to costly changes during construction.
Solution: Invest in Building Information Modeling (BIM) and thorough design reviews to catch errors early. Engage experienced architects and engineers to verify designs before approval.
3. Scope Creep and Change Orders
Scope creep occurs when additional work is requested beyond the initial contract. While some changes may be unavoidable, unchecked modifications can inflate costs and extend timelines.
Solution: Establish a strict change management process and use contract clauses to define scope changes clearly. Require stakeholder approvals before initiating scope modifications.
4. Unforeseen Site Conditions
Unexpected underground utilities, soil instability, or environmental hazards can increase costs significantly.
Solution: Conduct geotechnical surveys, environmental assessments, and utility mapping before breaking ground. Allocate contingency funds for unpredictable site issues.
5. Poor Project Management
Miscommunication, scheduling conflicts, and lack of coordination between teams can delay work and increase labor costs.
Solution: Implement construction project management software to track progress, manage schedules, and improve communication. Use agile project management techniques to adapt to challenges efficiently.
6. Inflation and Market Fluctuations
Material and labor costs can spike due to global economic conditions, trade tariffs, or supply chain disruptions.
Solution: Lock in pricing with suppliers through long-term procurement agreements and include contingency funds. Monitor economic trends to anticipate potential cost increases.
7. Legal and Regulatory Issues
Compliance with local building codes, zoning laws, and environmental regulations can lead to unexpected costs if not addressed early.
Solution: Engage legal experts during project planning to ensure compliance and avoid penalties. Create a dedicated compliance team to track changes in regulations.
Real-World Examples of Construction Cost Overruns
Sydney Opera House, Australia
- Initial Budget: $7 million
- Final Cost: $102 million
- Cause: Poor planning, frequent design changes, and unforeseen challenges.
Boston’s Big Dig, USA
- Initial Budget: $2.8 billion
- Final Cost: $8 billion
- Cause: Mismanagement, unexpected geological conditions, and regulatory changes.
Berlin Brandenburg Airport, Germany
- Initial Budget: €2 billion
- Final Cost: €7.3 billion
- Cause: Design flaws, contractor disputes, and regulatory issues.
SoFi Stadium, USA
- Initial Budget: $2.6 billion
- Final Cost: $5.5 billion
- Cause: Rising material costs, scope changes, and permitting delays.
Strategies to Prevent Cost Overruns
1. Accurate Cost Estimation
Use modern estimating software to generate precise, data-driven cost projections. Regularly update estimates as project variables change.
2. Strong Contract and Change Order Management
Clearly define project scope and establish change control procedures to prevent scope creep and uncontrolled modifications.
3. Robust Project Management Practices
Adopt construction management software such as Planyard to track project costs, manage budgets, and ensure timely execution.
4. Detailed Site Assessments
Perform soil tests, environmental assessments, and feasibility studies before construction to minimize unexpected conditions.
5. Supplier and Contractor Coordination
Work with reliable suppliers and contractors who have a track record of delivering on time and within budget.
6. Regulatory Compliance Planning
Stay informed about industry regulations, secure necessary permits early, and consult legal experts to avoid costly compliance issues.
7. Contingency Planning
Set aside at least 10-20% of the total project budget as contingency funds for unexpected expenses.
Role of Software in Cost Overrun Prevention
Construction management software, like Planyard, helps reduce cost overruns by providing:
- Real-time budget tracking
- Automated cost reporting
- Purchase order and invoice management
- Collaboration tools for teams and subcontractors
- AI-driven forecasting and cost prediction
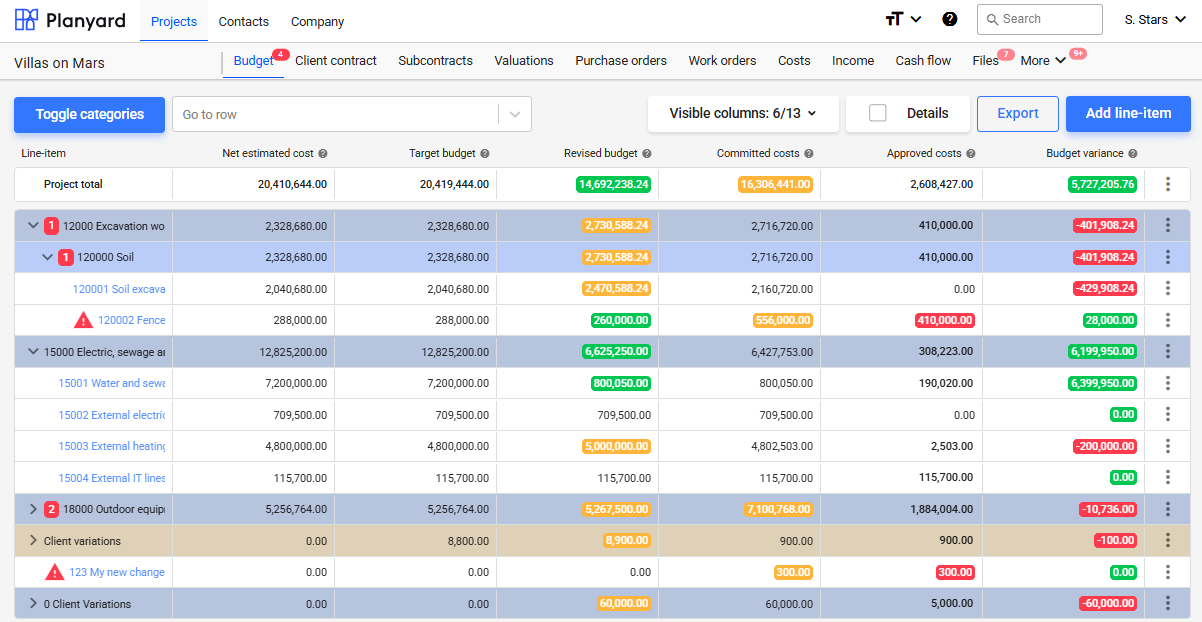
Conclusion
Construction cost overruns remain a significant challenge, but with careful planning, advanced project management tools, and strict financial oversight, they can be minimized.
By leveraging construction project management software like Planyard, firms can track costs in real time, ensure better budget adherence, and complete projects more efficiently.