A Bill of Quantities (commonly referred to as a BoQ or BQ) is a vital document in the construction industry, especially for larger projects. Prepared by a quantity surveyor (QS) or cost consultant, it lists and quantifies the work needed to complete a construction project. By defining not just the quantities but also the quality and scope of the required tasks, the BoQ ensures fair and transparent tendering, simplifies cost management, and provides a systematic way to manage changes and final valuations.
What Does “BoQ” Mean?
BoQ stands for Bill of Quantities, which is essentially a detailed breakdown of a project’s scope. It typically includes:
- Item Descriptions: A clear outline of each work item or element.
- Measured Quantities: These can be in numbers, lengths, areas, volumes, weights, or time, depending on the nature of the work.
- Work Sections: Often aligned with standard methods of measurement (e.g., NRM2, CESMM for civil works).
- Rates or Prices: Space for tenderers to insert their prices, forming the basis for cost evaluation.
This document is generally issued during the tender stage, helping contractors price the works accurately without having to measure everything themselves from scratch. It fosters consistency and makes the comparison of tenders more straightforward.
What Is Included in a Bill of Quantities?
A well-structured Bill of Quantities typically encompasses:
- Preliminaries
These outline the general conditions of the project, such as site rules, health and safety requirements, contractual obligations, and other preliminary aspects that apply to all work sections. - Measured Work Items
Each construction element (e.g., substructure, superstructure, finishes, services) is measured and itemised according to a standard methodology like NRM2 (New Rules of Measurement) or CESMM (Civil Engineering Standard Method of Measurement).- Substructure might include excavation, foundations, damp-proof membranes, etc.
- Superstructure might encompass walls, roof structures, windows, and so forth.
- Schedules of Rates (if applicable)
Certain BoQs include a schedule of rates that can be used for pricing variations or additional work during the construction phase. - Contingency Sums
A contingency sum allows for unforeseen costs. Sometimes it’s a lump sum, while in other cases it covers a specific element where the extent of work isn’t entirely clear at tender stage. - Provisional Sums and Provisional Quantities
These are included when the exact details or quantities of certain works cannot be precisely measured at the time of tender. They help manage potential changes without needing an immediate variation order. - Dayworks or Prime Cost Items (if relevant)
For certain specialised services or works, there may be prime cost (PC) items or daywork rates to cover trades that are measured and paid for by the hour, plus materials.
By laying out details in this manner, the BoQ becomes a roadmap for contractors, subcontractors, and the design team to follow throughout the project.
BoQ vs. BOM (Bill of Materials) – What’s the Difference?
Although both documents detail items required for a project, they serve distinct purposes:
- Bill of Quantities (BoQ)
- Emphasises measured works, including labour, overheads, plant, and materials.
- Used extensively in construction for tendering, costing, and contract management.
- Follows standard rules of measurement to enable fair tender comparisons.
- Bill of Materials (BOM)
- More prevalent in manufacturing or product assembly contexts.
- Focuses on listing components or materials needed, often without specifying the associated labour or method of installation.
- Less likely to be broken down by work sections and more geared towards the procurement of parts.
Essentially, a BoQ covers the ‘who, what, and how’ of installing each item in a construction setting, whereas a BOM is primarily about the materials themselves—often used in engineering or product fabrication processes where labour is accounted for separately.
How to Calculate a Bill of Quantities
Preparing a BoQ is a methodical process, usually undertaken by a quantity surveyor or an experienced cost consultant. Below is a simplified outline of the steps involved:
- Complete the Design and Specification
- Ensure that architectural drawings, structural details, and any specialist design elements are ready.
- The specification should define materials, finishes, and workmanship standards.
- Take Off Quantities
- “Taking off” refers to extracting measurements from the project drawings and specifications.
- Standard units (e.g., m² for walls, m³ for concrete) are used to maintain consistency.
- Breaking down work items by section or trade makes it easier to distribute works among potential subcontract packages.
- Organise the Information
- Group the measured items under appropriate headings (preliminaries, substructure, superstructure, services, finishes, etc.) according to the chosen method of measurement (e.g., NRM2).
- If the project involves civil engineering elements, use CESMM4 to ensure uniformity with industry standards.
- Assign Rates and Prices
- Either use historical cost data, supplier quotes, or subcontractor rates to price each measured item.
- Make allowances for overheads, profit, and potential risks—such as fluctuations in material costs.
- Include Contingencies and Provisional Sums
- Carefully consider any uncertain areas of the design or site conditions.
- Provide for provisional sums in the event certain details are refined later.
- Compile, Check, and Finalise
- Verify all calculations to reduce the risk of errors or omissions.
- Ensure any special requirements match the specification and drawings.
- Present the final Bill of Quantities as part of the tender documentation.
Practical Tips:
- Use Standard Rules of Measurement: This avoids ambiguity and minimises contractual disputes later.
- Cross-Reference with Drawings: Double-check that each measured element is present on the plans and in the specification.
- Leverage Software: Modern construction software or BIM (Building Information Modelling) tools can generate BoQs more swiftly, although a QS’s professional judgement is still essential.
- Early Contractor Engagement: If possible, consult with contractors or subcontractors for more accurate estimating. Real-world insights can reduce unnecessary contingencies.
Example Scenario: New Office Building
Imagine you are preparing the BoQ for a new three-storey office block. You would:
- Review the architectural and structural drawings thoroughly.
- Measure each element—foundations, columns, beams, floor slabs, walls, doors, windows, mechanical and electrical works, etc.
- Assign each item to a relevant work section (e.g., substructure for foundations, superstructure for walls and columns, finishes for flooring and painting).
- Ask your suppliers or sub-contractors for quotes to price the measured works accurately.
- Provide for a contingency sum to cover any unforeseen ground conditions or design changes.
Advantages of a Well-Prepared BoQ
- Fair Tendering: All contractors price the same list of items, ensuring a like-for-like cost comparison.
- Budget Certainty: The client obtains a clearer picture of overall costs and potential contingencies.
- Variation Control: As work proceeds, the BoQ helps value any changes and compute interim payments more efficiently.
- Transparency and Dispute Avoidance: A clearly structured BoQ, tied to standard measurement rules, reduces misunderstandings.
Avoiding Common Pitfalls
- Discrepancies
- Issue: If an item is in the design but missing from the BoQ (or vice versa), disputes can arise.
- Solution: Always cross-verify the BoQ against drawings and specifications before finalising.
- Underestimating Contingencies
- Issue: Skimping on contingencies can lead to budget and time overruns later.
- Solution: Factor in realistic allowances based on known project complexities.
- Reliance on Software Alone
- Issue: Automated tools can produce errors if the underlying data or model is incorrect.
- Solution: Combine software outputs with professional checks and site knowledge.
- Poor Coordination
- Issue: Inadequate communication among project stakeholders can result in conflicting measurements.
- Solution: Conduct regular coordination meetings and keep all parties updated on design changes.
Approximate Bills of Quantities
For projects where some design details are incomplete, an approximate Bill of Quantities (or notional BoQ) may be used. This offers indicative measurements for tendering but carries a higher risk of variations once final details are clarified. If actual quantities deviate significantly, contractors may be entitled to claim additional time or costs under the contract.
Enhancing BoQ Management with Planyard
A Bill of Quantities is a cornerstone of cost management and tendering in the UK construction industry. By measuring, itemising, and pricing each aspect of the works, it ensures tenderers compete on an even footing and provides clients with reliable cost data. Whether you are a property developer, a main contractor, or a subcontractor, understanding how to prepare, interpret, and utilise BoQs can greatly enhance the efficiency and transparency of your projects.
Managing Bills of Quantities (BoQs) manually can be time-consuming and error-prone. Planyard streamlines BoQ workflows with automation and real-time budget tracking, improving accuracy and efficiency:
- Real-Time Budget Updates – Upload your BoQ and let Planyard handle cost tracking automatically.
- Seamless Procurement Integration – Link BoQ items to purchase orders, subcontracts, and change orders effortlessly.
- No More Overbilling – Built-in approval workflows ensure payments match the agreed quantities and rates.
- Instant CVR & Forecasting – Get real-time insights into cost variations and financial health.
- Clear, Simple Reporting – One-click CVRs and forecast reports for full financial transparency.
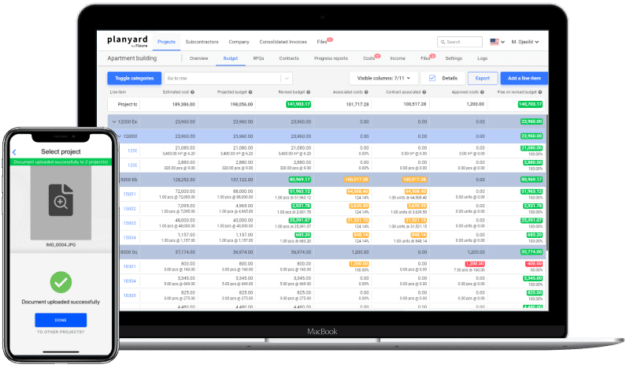
Book a demo to see how Planyard can simplify your BoQ management, or try it free for 14 days!