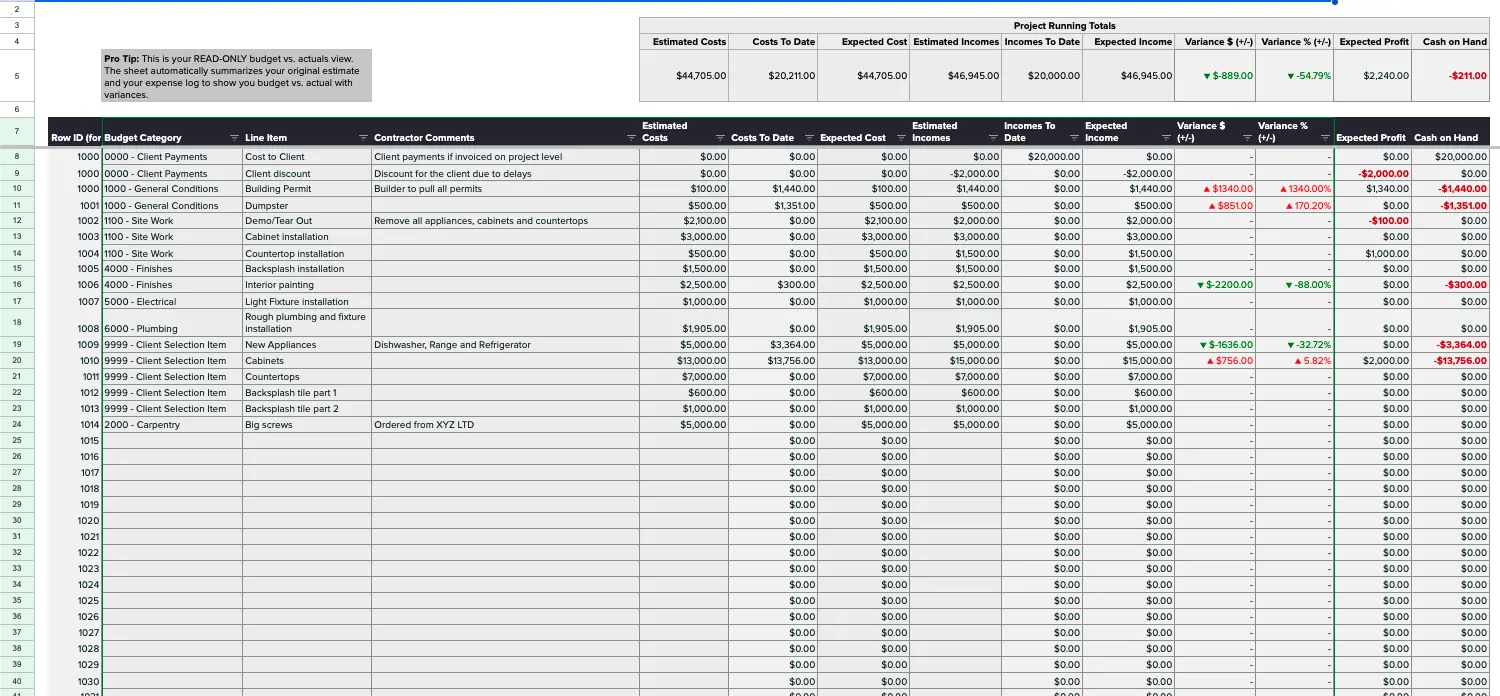
Managing finances effectively is critical for any construction project. A well-designed construction budget template is a powerful tool to plan, track, and manage expenses efficiently. Whether you’re working on a small residential build or a large-scale commercial project, our templates help ensure every dollar is accounted for.
This explanation provides actionable insights into construction budget templates, answers critical questions, and highlights how tools like Planyard can enhance your budgeting process.
What Is a Construction Budget Template?
A construction budget template is a structured framework designed to help project managers and contractors plan, track, and control the financial aspects of a construction project. By organizing costs into clear categories and subcategories, these templates provide a comprehensive overview of a project’s financial health, ensuring that every dollar is accounted for from start to finish.
Why Is a Construction Budget Template Important?
- Financial Clarity: A well-designed template outlines all costs, from pre-construction planning to final execution, providing a clear view of the project’s financial scope.
- Improved Decision-Making: By comparing estimated, committed, and actual costs, project managers can identify variances and take corrective actions proactively.
- Error Reduction: Using a standardized template minimizes the risk of errors common with ad hoc spreadsheets or manual calculations.
- Collaboration: Templates simplify communication among stakeholders by presenting financial data in an easy-to-understand format.
Who Benefits from a Construction Budget Template?
- Project Managers: Gain control over expenses and ensure projects stay on budget.
- Contractors: Improve profitability by tracking labor, materials, and subcontractor costs.
- Clients and Stakeholders: Receive transparent insights into how funds are allocated and spent.
In essence, a construction budget template is the foundation of financial management for any project, ensuring that resources are used efficiently and outcomes remain predictable. By starting with a structured template, you reduce uncertainty and set the stage for a successful build.
How Do You Create a Budget for a Construction Project?
Creating a construction budget involves several stages, each requiring careful attention to detail. A construction budget ensures financial control and helps avoid cost overruns, making it a crucial element in any project’s planning phase. Here’s a step-by-step guide to creating a comprehensive construction budget:
1. Define the Project Scope
Start by outlining the project’s goals, deliverables, and timelines. The scope should clearly define what is included in the project to avoid misunderstandings or unexpected costs.
2. Break Down the Work Structure
Divide the project into smaller components, often called a Work Breakdown Structure (WBS). Each component represents a specific phase, milestone, or deliverable, such as site preparation, foundation, framing, and finishing.
3. Identify Cost Categories
Separate costs into categories such as labor, materials, equipment, subcontractor fees, permits, and overhead. This categorization simplifies the tracking and allocation of expenses later.
4. Collect Data for Cost Estimation
Gather pricing data from the following sources:
- Past Projects: Use historical data to estimate costs for similar activities.
- Supplier Quotes: Obtain quotes for materials and equipment.
- Labor Rates: Calculate hourly or daily rates for workers and subcontractors.
5. Allocate Contingency Funds
Set aside a contingency fund to cover unexpected expenses. The industry standard is typically 10–15% of the total estimated budget.
6. Use a Template or Digital Tool
A construction budget template or a specialized tool like Planyard ensures your budget is organized and allows for real-time updates as the project progresses.
7. Review and Adjust Regularly
Budgets are dynamic and should be reviewed periodically. As the project evolves, update estimates and adjust for changes in scope or market conditions.
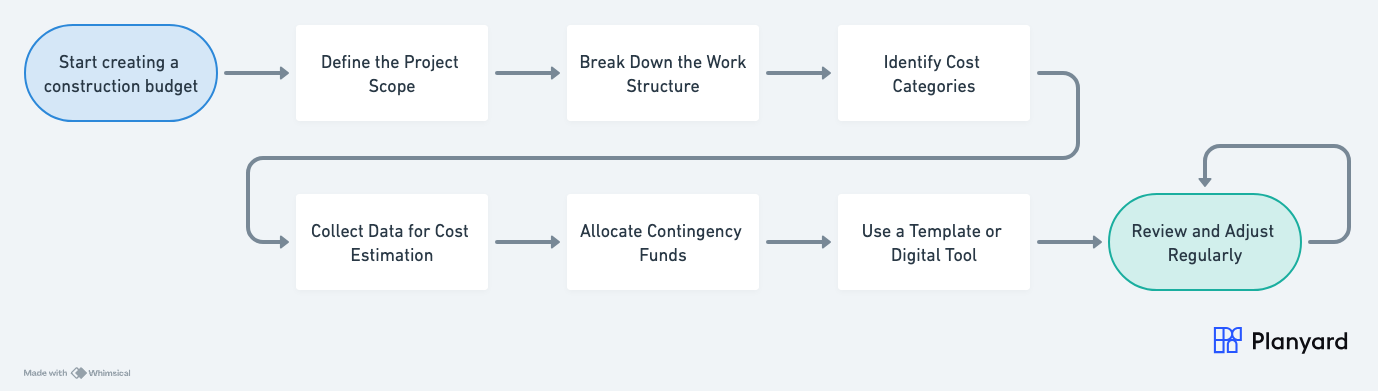
What Is Included in a Construction Budget?
A construction budget is a comprehensive document that encompasses all financial aspects of a project. Each category should be carefully detailed to ensure accurate tracking and prevent oversights. Below are the primary components:
1. Labor Costs
Labor includes wages for workers, subcontractor fees, and benefits. It’s one of the largest portions of a construction budget. Labor costs can vary depending on:
- The complexity of tasks.
- The size of the workforce.
- Regional wage differences.
2. Materials
This category covers all raw materials required for construction, such as concrete, steel, lumber, and fixtures. It also includes transportation costs and any wastage allowances.
3. Equipment
Costs for equipment include rentals, purchases, maintenance, and fuel. Heavy machinery like cranes or excavators often falls under this category.
4. Subcontractor Fees
Specialized tasks such as electrical work, plumbing, and HVAC installations often require subcontractors. Their fees include labor and any specialized equipment they provide.
5. Permits and Licensing
Legal approvals like building permits and inspection fees ensure compliance with local regulations. These costs can vary significantly based on the project’s location and scope.
6. Administrative Overhead
Overhead includes project management salaries, office expenses, insurance, and utilities. These indirect costs are necessary to keep the project running smoothly.
7. Contingency Funds
Reserved for unexpected expenses, contingency funds are crucial for addressing unforeseen challenges like material price increases or design changes.
Category | Description | Key Considerations |
---|---|---|
Labor Costs | Wages, benefits, and overtime for workers and subcontractors | Varies by region, skill level, and project complexity |
Materials | Raw materials like concrete, steel, lumber, and fixtures | Account for waste, transportation, and supplier reliability |
Equipment | Costs for renting, purchasing, maintaining, and fueling heavy machinery | Include operational costs like fuel and operator fees |
Subcontractor Fees | Payments for specialized tasks like electrical work, plumbing, and HVAC installations | Ensure clear contracts detailing labor and material costs |
Permits & Licensing | Regulatory approvals and inspection fees | Costs depend on local laws and project scope |
Administrative Overhead | Indirect costs such as office expenses, insurance, and utilities | Allocate as a percentage of total direct costs |
Contingency Funds | Reserved for unexpected expenses or scope changes | Typically 10–15% of the total budget |
How Do You Calculate a Construction Budget?
Once the components of the budget are defined, the next step is to calculate costs for each category. This process involves estimating quantities, applying rates, and considering additional factors like taxes and contingencies. Here’s how calculations are typically done:
1. Calculating Labor Costs
Labor costs are calculated by multiplying the number of hours or days required by the hourly or daily wage rates.
Formula:
Labor Cost = (Number of Workers × Hours Worked) × Hourly Wage
Example:
- Number of workers: 10
- Hours per day: 8
- Wage per hour: $25
- Total labor cost for one week:
10 x 8 x 25 x 5 = $10,000
2. Calculating Material Costs
Material costs depend on quantities required and the unit price of each material. Include allowances for waste or excess.
Formula:
Material Cost = Quantity × Unit Price
Example:
- Concrete required: 50 cubic yards
- Cost per cubic yard: $150
- Total material cost:
50 x 150 = $7,500
3. Calculating Equipment Costs
For equipment, calculate rental costs based on the duration of use or amortization if purchased. Include operational costs like fuel and maintenance.
Formula:
Equipment Cost = (Rental Rate × Days Used) + Fuel & Maintenance
Example:
- Crane rental: $500/day
- Days used: 10
- Fuel and maintenance: $1,000
- Total equipment cost:
(500 x 10) + 1,000 = $6,000
4. Accounting for Subcontractor Fees
Subcontractor costs include both labor and materials provided by the subcontractor. Ensure these are detailed in their contracts.
5. Adding Overhead and Contingencies
Overhead is typically a fixed percentage (e.g., 10–15%) of direct costs. Contingencies are added to account for unforeseen circumstances, and calculated as a percentage of the total budget.
Step | Formula/Approach | Example |
---|---|---|
Labor Costs | Number_of_Workers x Hours_Worked x Hourly_Wage | 10 workers × 8 hours × $25/hour × 5 days = $10,000 |
Materials | Quantity x Unit_Price | 50 cubic yards × $150 = $7,500 |
Equipment Costs | (Rental_Rate x Days_Used) + Fuel_and_Maintenance | ($500/day × 10 days) + $1,000 = $6,000 |
Subcontractor Fees | Agreed fee for specific tasks (labor + materials) | Plumbing contract: $5,000 |
Permits & Licensing | Fixed costs based on local regulatory requirements | Building permits and inspection fees: $3,000 |
Contingency Funds | Percentage of total costs to cover unexpected expenses | 10% of the total budget: 10% x $31,350 = $3,150 |
These tables provide a concise overview of the key components and steps to calculate a construction budget, making it easier to structure and implement an effective budgeting process.
Example of the Final Budget
Here’s how the final budget might look after calculations:
Category | Calculation | Total |
---|---|---|
Labor | 10 workers × 8 hours × $25 × 5 days | $10,000 |
Materials | 50 cubic yards × $150 | $7,500 |
Equipment | (10 days × $500) + $1,000 | $6,000 |
Subcontractors | Plumbing work, fixed fee | $5,000 |
Permits & Licensing | Fixed fees | $3,000 |
Contingency (10%) | 10% of direct costs | $3,150 |
Total Budget | Add up the above | $34,650 |
By following these steps and utilizing detailed calculations, you can create a comprehensive, accurate construction budget that ensures financial control throughout the project.
What Is a Construction Cost Worksheet?
A construction cost worksheet is a detailed document used during the planning and execution phases of a project. It serves as a centralized tool to estimate, track, and analyze every cost incurred, ensuring that the project stays on budget.
This worksheet breaks down costs into categories and individual line items, showing estimated, actual, and committed costs. By comparing these figures, project managers can identify variances and take corrective action.
Why Is It Important?
- Visibility: Offers a granular view of project expenses, ensuring no hidden costs.
- Accountability: Tracks cost responsibilities for subcontractors, suppliers, and project owners.
- Proactive Management: Alerts to cost overruns early, allowing adjustments before they escalate.
Example of a Construction Cost Worksheet
Cost Category | Estimated Cost | Actual Cost | Variance | Responsibility |
---|---|---|---|---|
Labor | $10,000 | $12,000 | +$2,000 | Project Manager |
Materials | $7,500 | $5,500 | -$2,000 | Procurement Officer |
Equipment | $6,000 | $6,500 | +$500 | Site Supervisor |
Subcontractors | $5,000 | $5,000 | – | Project Manager |
Permits & Licenses | $3,000 | $2,800 | -$200 | Administrative Lead |
Contingency | $3,150 | $3,180 | +$30 | Project Accountant |
How to Use It Effectively
- Itemize Costs: Include all anticipated costs, even minor ones, to avoid surprises later.
- Monitor Variances: Regularly compare estimated and actual costs to track overruns.
- Integrate Technology: Use tools like Planyard to automate updates and ensure accuracy.
Why Planyard Is a Game-Changer for Construction Budgets
While traditional tools like Excel or free templates are helpful, they lack the flexibility and efficiency of modern software. Planyard offers advanced features tailored to construction professionals, making budget management seamless and precise.
Key Benefits
Feature | Traditional Methods | Planyard |
---|---|---|
Real-Time Tracking | Manual updates required | Automatic updates with live data |
Error Reduction | High risk of entry errors | Automated calculations and data entry |
Collaboration | Limited version control | Multi-user access with permissions |
Profitability Insights | Requires manual effort | Real-time forecasts and analytics |
Using Planyard ensures every dollar is accounted for, costs are tracked in real time, and profitability is maximized.