Construction estimating is the process of forecasting all costs involved in a construction project. This includes materials, labor, equipment, and indirect costs such as permits and overhead. It’s an essential practice for contractors and project managers, ensuring that projects are both financially feasible and profitable.
Accurate construction estimating minimizes risks, avoids budget overruns, and sets a strong foundation for project planning and execution.
The Importance of Construction Estimates
Accurate estimates ensure:
- Financial Planning: Aligning project goals with available budgets.
- Risk Mitigation: Preventing cost overruns by forecasting potential issues.
- Resource Optimization: Allocating manpower, materials, and equipment efficiently.
- Transparency: Building trust with clients through clear and well-documented costs.
Is Construction Estimating Hard to Learn?
The complexity of construction estimating depends on the project type, scale, and resources used. While some aspects might seem daunting at first, a structured approach and the right tools make it manageable.
Challenges in Learning
- Technical Knowledge: Understanding construction techniques, material properties, and equipment capabilities is essential.
- Costing Skills: Estimators need to be adept at calculating unit costs and labor productivity rates.
- Adaptability: Construction estimating must adapt to various projects, from residential construction estimating to large-scale infrastructure projects.
Why It’s Worth It
Mastering cost estimation in construction is a highly valued skill. Accurate estimates build trust with clients, enhance project management, and improve profitability.
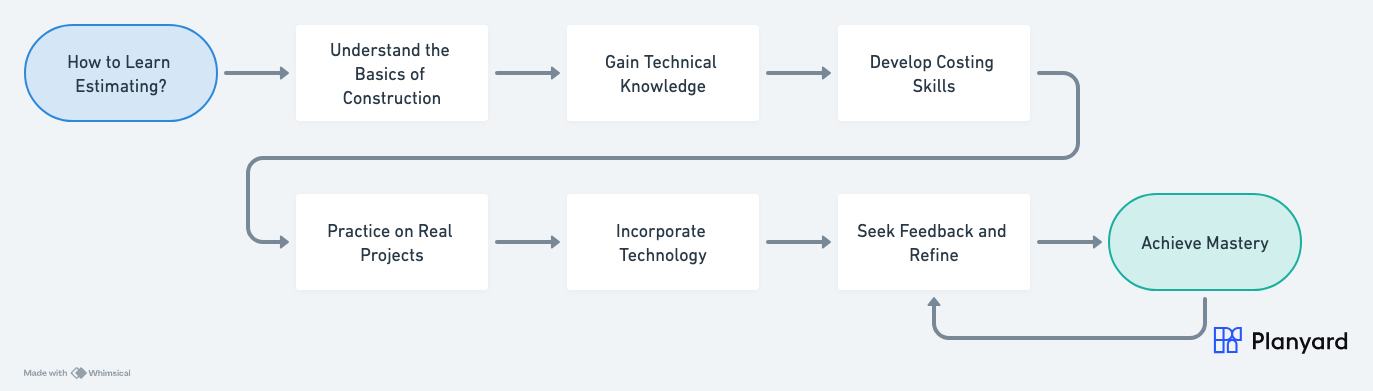
What Are the Three Types of Construction Estimates?
The type of estimate you prepare often depends on the project phase and its requirements. Understanding these distinctions helps contractors choose the right method for various scenarios.
Preliminary Estimates
Preliminary estimates are prepared during the early stages of a project. They provide a high-level construction budget estimate to evaluate feasibility. For example, if a developer is considering multiple locations for a new retail store, they might use preliminary estimates to compare costs like land preparation and permits.
Detailed Estimates
Detailed estimates are created when project plans and specifications are finalized. They break down costs into specific components like materials, labor, and subcontractor fees. These estimates are more accurate and are often used to secure financing or prepare bids. For general contractor estimates, detailed calculations ensure transparency and accuracy in pricing.
Bid Estimates
Bid estimates are developed by contractors competing for a project. They include all project costs and profit margins. Winning bids often highlight not just competitive pricing but also efficient project timelines. Using advanced tools like Planyard allows contractors to manage their construction estimating process efficiently, enhancing their ability to win projects.
Aspect | Preliminary Estimate | Detailed Estimate | Bid Estimate |
---|---|---|---|
Accuracy | Low to Moderate | High | High |
Use Cases | – Feasibility analysis- Early project planning | – Budgeting- Loan approval- Comprehensive cost analysis | – Competitive bidding- Winning contracts- Client presentations |
Preparation Phase | Early-stage, often conceptual | Mid-stage, after design and specifications are finalized | Final-stage, tailored for client and specific project requirements |
Inputs Required | Minimal details; relies on historical data or rough estimates | Detailed blueprints, material lists, and labor requirements | Finalized project scope, detailed cost breakdown, and markups |
Time to Prepare | Short | Moderate | Moderate to Long |
Level of Detail | Broad; focuses on approximate costs | Detailed breakdown of all components | Comprehensive with added profit margins and contingencies |
Examples | Comparing multiple site optionsInitial budgeting | Planning project fundingSetting detailed budgets | Submitting proposalsNegotiating contracts |
How to Calculate an Estimate in Construction?
Calculating an estimate in construction requires careful planning and detailed analysis. The process ensures all potential costs are accounted for, which reduces the likelihood of budget overruns. Here’s a deeper look at each step.
Reviewing Plans and Specifications
Begin by studying architectural blueprints, engineering drawings, and project specifications. These documents outline the scope of work, which forms the foundation of your estimate. A comprehensive understanding of the project’s requirements allows you to anticipate materials, equipment, and labor needs. For example, building cost estimates for a multi-story office will differ significantly from a single-family home due to varying structural and finishing demands.
Performing a Quantity Takeoff
Quantity takeoff involves calculating the volume of materials required. This includes everything from concrete for foundations to finishing items like tiles or paint. Precision in this step ensures your construction cost estimate reflects actual project needs, minimizing waste and shortages.
Determining Costs
Assign costs to each element of the project:
- Material Costs: Source quotations for all materials.
- Labor Costs: Factor in hourly wages, overtime, and any specialized expertise.
- Equipment Costs: Include rental or purchase prices, operational expenses, and maintenance. Knowing how to estimate equipment costs in construction is crucial for accuracy.
Adding Overhead and Contingencies
Indirect costs like administrative expenses, insurance, and utilities are added to the budget. Contingencies are included as a safeguard against unexpected expenses, typically ranging from 5–15% of the total cost.
Finalizing the Estimate
Review the calculations to ensure all elements are included. A finalized estimate should be structured clearly, with line items categorized and a total summary at the end. Tools like Planyard streamline this process by automating calculations and generating client-ready documents.
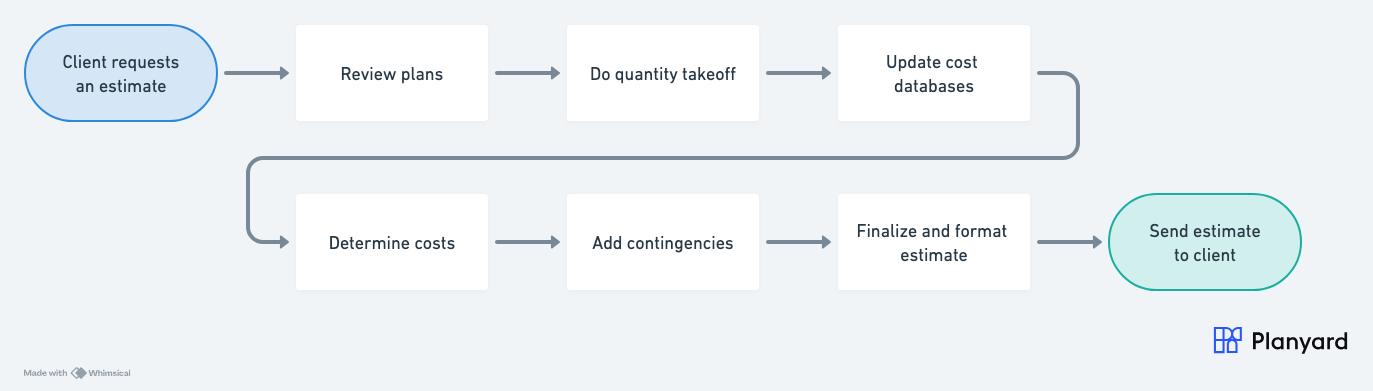
Best Practices for Estimating Building Costs
Estimating building costs accurately is both an art and a science, requiring a mix of historical knowledge, industry trends, and precise methodologies. Below are expanded strategies and insights to elevate your construction estimating process and ensure reliable outcomes.
Leverage Historical Data
One of the most effective ways to refine construction cost estimating is by analyzing historical project data. By reviewing records from previous similar projects, you can better understand typical cost patterns, potential overruns, and resource requirements.
- Benchmarking Costs: Historical data serves as a benchmark for materials, labor, and equipment costs. For instance, if a prior project of similar scope used 20 tons of steel at a specific cost, you can adjust for inflation and current market rates.
- Risk Identification: Past projects can also highlight common risks, such as underestimated labor hours or unexpected material shortages. Using this knowledge, you can include appropriate contingencies in your current construction budget estimate.
Adopt Technology to Streamline the Process
Modern software solutions, like Planyard, have revolutionized how contractors prepare building cost estimates. These tools eliminate manual errors, save time, and improve collaboration.
- Automation of Calculations: Tools like Planyard automate repetitive tasks such as markup application, tax calculation, and cost distribution across categories. This speeds up the process while reducing errors.
- Scenario Analysis: Advanced software enables you to create multiple versions of an estimate, allowing you to simulate various scenarios such as changes in material costs or labor availability. This feature is invaluable for projects with unpredictable variables.
Regularly Update Cost Databases
Market conditions in the construction industry are constantly changing. Materials like steel, lumber, and concrete are subject to price fluctuations due to supply chain issues, inflation, and demand surges.
- Material Cost Tracking: Subscribe to market reports or supplier updates to stay informed of material price trends. Using outdated prices in your construction cost estimates can lead to significant budget discrepancies.
- Labor Market Monitoring: Regularly evaluate labor rates in your region. Skilled labor shortages or high demand for trades like electricians can inflate costs unexpectedly.
- Review Annually or Quarterly: For companies handling multiple projects, ensure your cost libraries are reviewed at least quarterly. This keeps your estimates reflective of current realities.
Create a Detailed Estimation Structure
A well-organized estimate is key to maintaining accuracy and fostering client trust. Break down the estimate into clear categories and subcategories, covering every aspect of the project.
- Line Items for Transparency: Include individual line items for materials, labor, equipment, permits, and overhead. For example, a detailed residential construction estimating breakdown might separate roofing materials from labor costs to install them.
- Hierarchical Organization: Group related costs under main headings like “Structural Work,” “Interior Finishing,” and “Site Preparation.” This hierarchy simplifies both internal reviews and client presentations.
- Allow for Adjustments: Make your structure flexible enough to accommodate changes, whether adding a new task or adjusting quantities mid-project.
Factor in Contingencies and Overhead
No estimate is complete without allowances for unforeseen circumstances. Including contingencies ensures you’re prepared for unexpected costs without jeopardizing project profitability.
- Contingency Budgeting: Typically, contingencies range from 5–15% of the project’s total cost. For more complex projects, like commercial construction estimating, a higher contingency percentage might be warranted.
- Overhead Allocation: Administrative expenses, insurance, permits, and utilities should be included under overhead costs. Clearly itemize these to avoid ambiguity in your final construction estimates.
- Project-Specific Variables: For projects in remote areas, consider additional logistics costs such as transportation of materials or labor housing.
Incorporate Client-Specific Needs
Clients often have unique requirements that influence the estimate. A customized approach not only ensures accuracy but also strengthens client relationships.
- Customization for Materials: Some clients may request premium or sustainable materials, which can significantly impact building cost estimates.
- Timeline Adjustments: A client who requires an expedited timeline may incur additional costs for overtime labor or rush material orders. Factor these into the construction budget estimate.
- Client-Friendly Presentations: Use software to generate professional, client-ready documents that clearly explain how the estimate was built.
Collaborate with Stakeholders
Involving key stakeholders in the estimation process can help identify blind spots and refine cost projections.
- Subcontractor Input: Subcontractors often have specialized knowledge about materials or labor requirements, especially for unique tasks like HVAC installation or custom woodwork.
- Team Collaboration: Engaging project managers and site supervisors in the estimating process in construction ensures that the estimate aligns with on-ground realities.
- Client Feedback: Sharing preliminary estimates with clients allows for adjustments based on their feedback, reducing disputes during execution.
Validate and Review the Estimate
Once the estimate is complete, review it meticulously to ensure accuracy and consistency.
- Peer Review: Have a senior estimator or project manager review your construction estimate to catch potential errors.
- Cross-Check with Industry Standards: Compare your estimate against industry benchmarks to ensure it aligns with typical costs for similar projects.
- Finalize with Confidence: A validated estimate provides a strong foundation for budgeting and financial planning, enhancing your credibility with stakeholders.
Learn From Every Project
Continuous improvement is critical for refining your estimation process. After each project, compare the estimated costs with the actual expenses to identify discrepancies and areas for improvement.
- Post-Project Analysis: Evaluate which cost components deviated from the estimate and why. For instance, underestimating labor hours could indicate inefficiencies in estimating construction costs.
- Build a Feedback Loop: Use insights from completed projects to update your cost databases and refine future estimates.
Communicate Clearly and Professionally
A clear and detailed estimate builds trust with clients and ensures smooth communication throughout the project lifecycle.
- Visual Presentations: Use graphs, charts, and categorized summaries to make complex construction cost estimates easier to understand.
- Explain Key Assumptions: Highlight any assumptions or limitations that may affect the estimate’s accuracy, such as uncertain material prices or weather-dependent timelines.
- Provide Flexibility: Offer clients the option to adjust certain aspects, such as material grades or timelines, to meet budget constraints.
By implementing these best practices, contractors and estimators can enhance the accuracy, efficiency, and professionalism of their construction estimating process, paving the way for successful projects and satisfied clients.
Common Mistakes in Construction Estimating
Construction estimating is a critical step in project planning, but it’s also susceptible to errors that can result in budget overruns and delays. Here are common mistakes contractors and estimators face and strategies to avoid them:
Underestimating Material Quantities
One of the most frequent errors is underestimating the quantity of materials needed for a project. This often occurs due to rushed quantity takeoffs or incomplete blueprints. For example, missing a column in a structural drawing can lead to significant cost increases later.
How to Avoid It:
- Conduct detailed quantity takeoffs using accurate and updated blueprints.
- Use construction estimation software like Planyard, which automates calculations and ensures nothing is missed.
Ignoring Indirect Costs
Indirect costs such as permits, administrative expenses, or equipment maintenance are often overlooked, leading to budget gaps. These costs can account for a substantial portion of the total budget in large projects.
How to Avoid It:
- Always include a section for indirect costs in your construction budget estimate.
- Review past projects to identify recurring indirect expenses.
Using Outdated Pricing Data
Material and labor costs fluctuate due to market dynamics. Using outdated pricing can lead to significant discrepancies between estimated and actual costs.
How to Avoid It:
- Update your cost database regularly by consulting suppliers and market reports.
- Utilize tools like Planyard, which integrates real-time cost tracking.
Neglecting Labor Productivity
Failing to account for realistic labor productivity rates often results in underestimated labor costs. Delays caused by unforeseen weather conditions, staff shortages, or site complexities further exacerbate the issue.
How to Avoid It:
- Use industry benchmarks for labor productivity and adjust for project-specific factors like site conditions.
- Include contingency plans for potential delays.
Overlooking Contingencies
Many estimators neglect to add a contingency buffer, which leaves no room for unexpected costs such as material waste or design changes.
How to Avoid It:
- Allocate 5–15% of the project’s total cost for contingencies, depending on the project’s complexity.
Relying on Manual Processes
Spreadsheets and manual calculations are prone to errors and inconsistencies, especially in large-scale projects.
How to Avoid It:
- Transition to digital construction estimating software that automates calculations and reduces errors.
By identifying and addressing these common pitfalls, contractors can create more reliable and accurate construction cost estimates, leading to smoother project execution and better client relationships.

The Importance of Accuracy in Construction Budget Estimates
Accurate construction budget estimates are essential for ensuring project success. They serve as a roadmap for financial planning, resource allocation, and stakeholder communication. Here’s why precision matters and how to achieve it:
Prevents Cost Overruns
Accurate estimates set a realistic financial framework for the project. Miscalculations, such as underestimating material costs, can lead to overruns that strain client-contractor relationships.
Key Tip: Use detailed breakdowns for materials, labor, and equipment to build a comprehensive budget. Tools like Planyard can automate these calculations for accuracy.
Enhances Resource Allocation
Precise estimates ensure resources are allocated efficiently, minimizing waste. For example, knowing the exact quantity of steel for a foundation helps avoid excess ordering and reduces project costs.
Key Tip: Rely on historical data and construction estimating guides to refine your quantity takeoffs and resource planning.
Builds Client Trust
Transparent and accurate estimates help build confidence with clients, showing professionalism and attention to detail. Providing a clear breakdown of costs demonstrates that you’ve thoroughly analyzed the project requirements.
Key Tip: Always include explanations for major cost items and highlight any assumptions made in the estimate.
Supports Financial Planning
Budget estimates impact cash flow management, loan approvals, and profitability forecasting. An inaccurate estimate can lead to financial bottlenecks that disrupt project timelines.
Key Tip: Integrate estimation tools with accounting systems to maintain real-time financial visibility.
By ensuring accuracy in construction budget estimates, contractors can reduce risks, avoid disputes, and enhance project profitability.
How Market Trends Influence Construction Cost Estimation
The construction industry is heavily influenced by market trends, which can directly impact construction cost estimates. Staying ahead of these trends ensures estimates remain competitive and accurate. Here’s how market dynamics affect cost estimation and tips to adapt:
Material Price Fluctuations
Global supply chain disruptions, inflation, and demand spikes can cause material prices to soar. For instance, the cost of lumber doubled in certain regions during the pandemic, significantly impacting building cost estimates.
How to Adapt:
- Establish relationships with multiple suppliers to negotiate better prices.
- Use software like Planyard to update material costs in real time.
Labor Market Dynamics
Skilled labor shortages drive up wages, especially for specialized roles like electricians or masons. This can make estimating construction costs challenging in labor-intensive projects.
How to Adapt:
- Incorporate realistic labor rates in your estimates.
- Include provisions for overtime or subcontractors to address shortages.
Regulatory Changes
New regulations, such as safety standards or environmental compliance, can add unexpected costs to projects. These are especially relevant in commercial construction estimating, where compliance is strict.
How to Adapt:
- Stay informed about local and international regulatory updates.
- Include compliance costs as a separate line item in your construction estimate.
Sustainability Demands
Green building practices are on the rise, with clients increasingly requesting sustainable materials and energy-efficient designs. These can raise upfront costs but often lead to long-term savings.
How to Adapt:
- Offer clients options for sustainable materials and include their cost implications in the estimate.
- Highlight how these choices align with long-term value to justify their inclusion.
Technological Advancements
Automation and prefabrication methods are reducing costs in certain areas while requiring upfront investment in specialized equipment. These innovations can shift the cost structure of a project.
How to Adapt:
- Explore opportunities to use cost-saving technologies, such as 3D printing for specific elements.
- Reflect these adjustments in your construction project cost estimation.
By understanding and responding to market trends, contractors can ensure their construction cost estimates remain accurate, competitive, and aligned with industry standards.
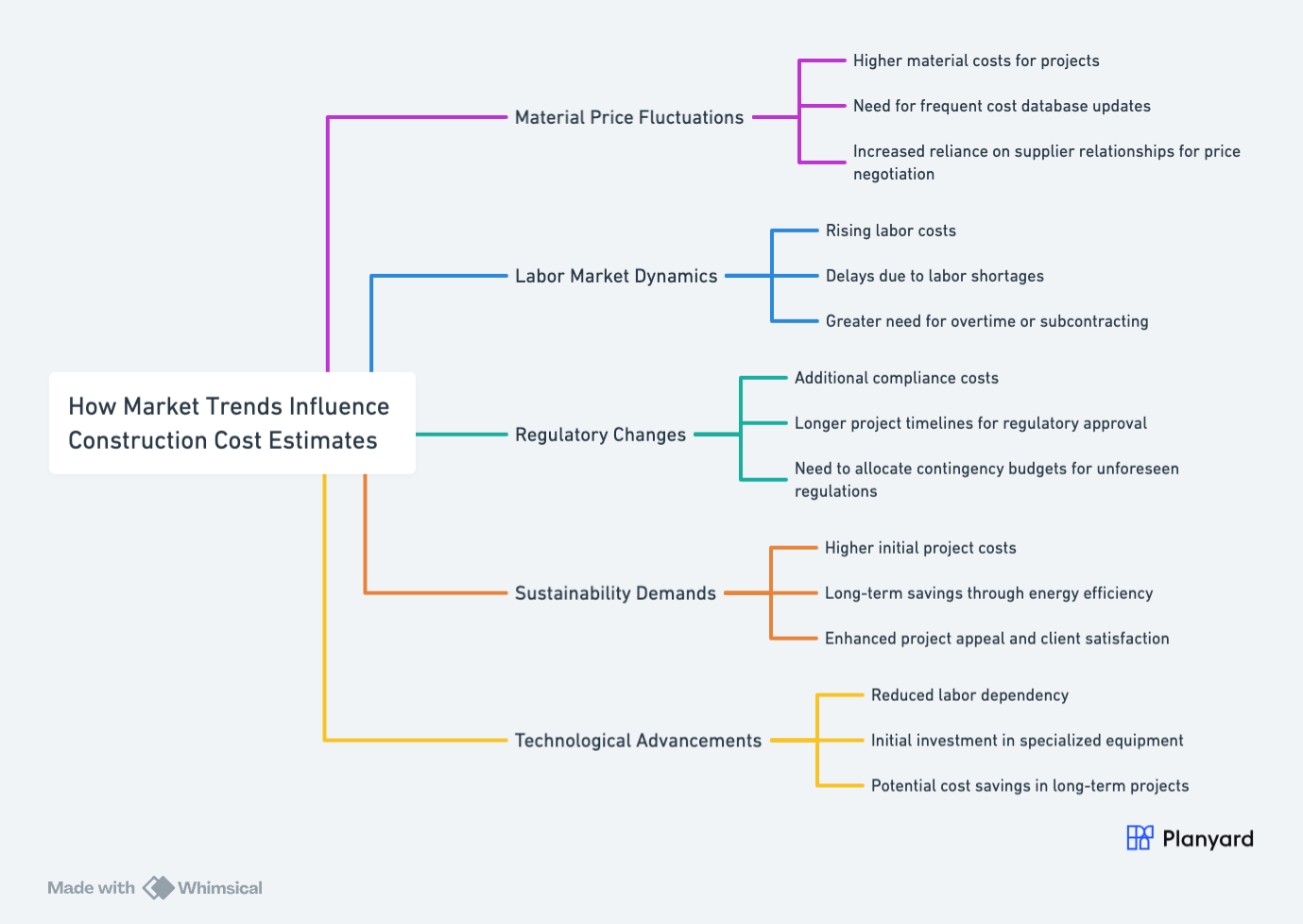
How to Estimate Construction Costs for Different Types of Projects
Residential Construction Estimating
Residential projects typically involve lower budgets but greater attention to detail. For example, a home renovation requires precise material costing to avoid wastage. Items like flooring, kitchen cabinets, and fixtures often dominate the budget. Labor costs are usually calculated per hour or task. Using construction estimating guides, contractors can adjust costs for regional variations in material prices and wages.
Commercial Construction Estimating
Commercial projects are larger in scope and complexity. Estimating construction costs for these projects involves additional considerations:
- Regulatory Compliance: Costs associated with permits and inspections.
- High-End Materials: Commercial projects often require durable, high-quality materials like reinforced steel or fire-resistant drywall.
- Specialized Labor: Employing skilled trades for installations like HVAC systems.
Equipment Cost Estimation
When estimating equipment costs, include:
- Rental rates for machinery.
- Fuel and maintenance costs.
For example, estimating how to calculate building construction costs for a high-rise often includes cranes, scaffolding, and material lifts.
Aspect | Residential Construction | Commercial Construction | Equipment Cost Estimation |
---|---|---|---|
Scope | Smaller-scale, focuses on homes or apartments. | Larger-scale, includes office buildings, retail spaces, and industrial facilities. | Involves calculating the costs of machinery and tools needed for construction projects. |
Key Cost Drivers | – Materials: Flooring, cabinetry, fixtures.- Labor: Skilled trades like carpenters and electricians.- Permits and fees. | – Materials: High-grade steel, concrete, fire-resistant materials.- Regulatory compliance and permits.- Specialized labor like HVAC technicians. | – Rental or purchase costs.- Fuel and maintenance expenses.- Operator training or labor costs. |
Accuracy Requirements | Moderate to high: Clients typically expect detailed budgets for personal investments. | High: Requires precise budgeting for large financial commitments and strict timelines. | Moderate: Equipment costs are often fixed, but fuel and maintenance can fluctuate. |
Challenges | – Customization requests.- Frequent design changes.- Regional material cost variations. | – Compliance with complex regulations.- Managing subcontractors.- Higher upfront material costs. | – Choosing between renting or purchasing.- Predicting long-term usage to calculate depreciation. |
Software and Tools | – Tools for residential takeoffs and material lists.- Budgeting templates for home renovations. | – Advanced estimating software with features for project phasing and cost tracking. | – Specialized software for tracking equipment usage, depreciation, and operational costs. |
Examples | – Single-family home construction.- Apartment renovations. | – Office building construction.- Multi-storey retail complexes. | – Crane rental for high-rise buildings.- Bulldozers for site preparation. |
Challenges in Construction Estimating
Despite its importance, construction estimating presents several challenges:
- Material Price Volatility: Frequent price changes due to market conditions.
- Labor Shortages: Increased demand for skilled workers often inflates costs.
- Scope Changes: Adjustments to project requirements can disrupt estimates.
- Manual Errors: Dependence on spreadsheets increases the likelihood of inaccuracies.
- Project Complexity: Coordinating multiple subcontractors and timelines adds layers of difficulty.
Streamlining Estimating With Technology
Modern software tools like Planyard have revolutionized construction estimating, helping teams overcome traditional challenges.
How Planyard Supports Estimation
Planyard is a cloud-based solution tailored to simplify construction cost estimation and budgeting. With features like automated calculations, centralized bid management, and real-time updates, it eliminates the inefficiencies of spreadsheets.
Key Benefits of Using Planyard:
- Efficiency Gains: Automate time-consuming tasks like cost calculations and bid adjustments.
- Error Reduction: Replace manual inputs with precise automated processes.
- Seamless Collaboration: Share estimates across teams, ensuring consistency.
- Real-Time Budget Conversion: Instantly turn winning bids into live project budgets, keeping financial tracking accurate throughout the project lifecycle.
A Professional Approach to Construction Estimating
Mastering construction estimating is essential for delivering profitable, on-schedule projects. While traditional methods can suffice for small-scale work, complex projects demand precise forecasting and efficient workflows. Tools like Planyard not only streamline the process but also improve accuracy, reducing errors and costly oversights.
By integrating advanced estimating software into your operations, you enhance efficiency, foster collaboration, and gain a competitive edge. These improvements are pivotal for general contractors, project managers, and construction firms aiming for long-term growth and profitability. Whether estimating for residential, commercial, or industrial projects, leveraging digital tools ensures scalability and professional excellence in construction cost management.